Fully functional loudspeaker is 3D-printed
December 17, 2013
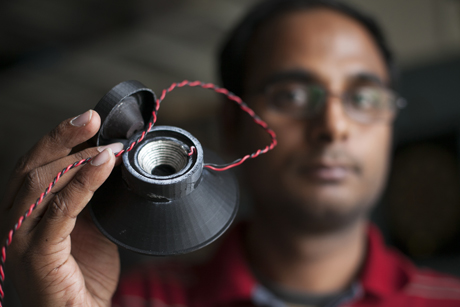
A 3D-printed, fully functional loudspeaker (credit: Jason Koski/Cornell University Photography)
The loudspeaker is a project led by Apoorva Kiran and Robert MacCurdy, graduate students in mechanical engineering, who work with Hod Lipson, associate professor of mechanical and aerospace engineering and a leading 3-D printing innovator.
The researchers used two Fab@Home printers, which are customizable research printers developed by Lipson that allow for tinkering with different cartridges, control software, and other parameters.
For the conductor, they used a silver ink and for the magnet, they developed a viscous blend of strontium ferrite.
[+]
Lipson said he hopes this simple demonstration is just the “tip of
the iceberg.” 3-D printing technology could be moving from printing
passive parts toward printing active, integrated systems.
Fab@Home (credit: Cornell)
But it will be a while before consumers are printing electronics at home, he cautioned. Most printers cannot efficiently handle multiple materials.
It’s also difficult to find mutually compatible materials — for example, conductive copper and plastic coming out of the same printer require different temperatures and curing times. Semiconductors are also a challenge.
(¯`*• Global Source and/or more resources at http://goo.gl/zvSV7 │ www.Future-Observatory.blogspot.com and on LinkeIn Group's "Becoming Aware of the Futures" at http://goo.gl/8qKBbK │ @SciCzar │ Point of Contact: www.linkedin.com/in/AndresAgostini